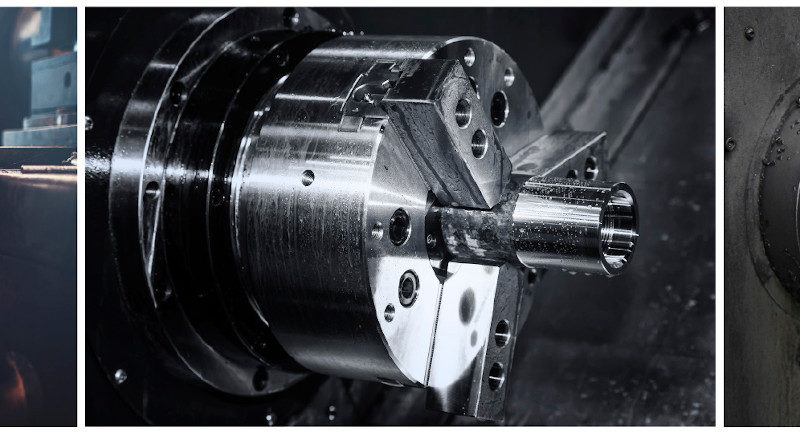
The lathe is one of the machine tools of greater demand of the market, both in maintenance workshops and machining production factories. In this guide you will evaluate the essential aspects to take into account to choose the right machine.
Sometimes, the acquisition of a new machine involves a group of questions that must be solved in the most convincing way possible, answering each one of them as accurately as possible. It is necessary to understand the purchase as an investment, since once your purchase is made, it becomes part of the assets of the company itself, so choosing the right lathe is vital to ensure the longevity of the company, because the production and products quality will depend directly on the performance of the machine.
On one hand, it is necessary to ask yourself three essential questions: what type of operation is intended to be performed with the lathe?, what number of pieces per a given period of time can be manufactured with the lathe?? and related to the previous two points: which amortization period is feasible for the company?.
On the other hand, when working with metals, there are fundamental issues to consider?
In relation to the characteristics of the machine itself:
Main motor power: From a power up to 350 Watts, a lathe will allow professional working. You also should have to take into account the maximum external diameter allowed, to know the workpieces size that can be manufactured or modified.
Swing Diameter over bed and swing diameter over carriage: if the lathe technical specifications sheet tells us that the maximum bed diameter allowed is 660 mm, we can fix it on the plate, but we can only perform some machining operations. If this piece we have to cylinder in its entire length, we can not work properly, because we have to take into account 2 variables:
The sliding carriage on the bed has a thickness to be considered.
The turret where the cutting tool is placed also occupies space.
Distance between centers: The distance between centers is measured between the chuck and the tailstock. Obviously, depending on the pieces and lengths to be machined, it is essential to choose the right lathe to the size of the piece with which it is intended to work, as well as choose the necessary supports if the goal is to work long pieces, there are steady and follow rests.
Automatic speed adjustments and feed speeds: There is the possibility that, based on a control of production and specific work operations, it is required that a lathe presents characteristics that allow continuous working without stopping the process. It is very useful the possibility of modifying the rotation speeds of the main spindle through a variator, allowing the work in different speed ranges, without needing to handle changes through levers.
PARALLEL LATHE
Variator detail. We observe two speeds: A and B.
Sliding Guideways:
They should be considered as one of the most important lathe parts. They act as a seat and the precision of the lathe depends directly on them. In the case of a second-hand machine, the guides tend to have uneven wear. One way to check the uniformity of the wear of the guides would be the following:
1st) Move the carriage towards the head and tighten the clamp.
2nd) Loosen it enough, allowing movement.
3rd) Move the carriage under the head.
It is advisable to measure the precision of the same with a comparative clock, in another post, we will explain the steps that we use in our assembly line to guarantee the accuracy before preparing a machine.
Heller lathe guides are hardened and ground to ensure their accuracy and longevity.
Head:
The head power is of vital importance when choosing a lathe, based on the operations to be made, we can determine if we need more or less power, if we are going to rough or start a lot of chips in each pass, it is advisable to select a very powerful head. If on the other hand, we want to start a little material, cylinder, or finish parts, so much power is not necessary.
Both the material to be machined and the work to be done must be taken into account when choosing the lathe head.
Gear Train and rear gears:
The gears play an essential role in lathe’s operation. When working with the machine, the noise determines if the adjustment, quality of the gears is appropriate, can also be checked by opening the top cover of the lathe head.
Our gears are of high hardness steel, carved with the best machines, hardened to 60HRC * and rectified.
- Rockwell hardness nomenclature, where the number 60 indicates the hardness value obtained, HR is the identifier of the Rockwell test, and the letter C refers to high strength steels.
Charriage, Tool Holder and Dimensions Digital Readout:
The charriage is the main element of displacement of the lathe and vital for carrying out machining. In addition to its cutting function, it incorporates the measurement scales to do a correct job. In the case of our lathes, we also install a standard Fagor visualizer that allows electronic control of up to 4 decimals of the displacements that are made, as well as ensuring greater precision, facilitates the work of the operator, as it can see more clearly and it needs the displacements that it is making.
Finally, in Follow conventional lathes we always install a robust turret with quick change, ensuring rigidity of the tool, something essential to have good finishes in workpieces. This type of turret allows a high speed of change and the housing of 4 toolholders square of 25mm.
And, a CNC lathe?
When it comes to acquiring a lathe, it is worth asking as with other types of machine tools, if the most interesting option would be a numerical control model. Obviously, this decision must be taken taking into account the conditions of production in the company (workload, work cycles, level of finish and precision required in the parts ?) as well as the level of automation desired.
What advantages would the use of a CNC lathe have compared to a conventional lathe?
It requires less staff: A single operator can manage several CNC lathes when working autonomously, initially you have to use time in your programming, then work autonomously without the need of an operator immediately present. The traffic light indicates the state of the cycle to notify operators when the piece is finished and can be replaced by a new one to continue producing.
Increased precision: Unlike the conventional lathe, where the finishes depend to a great extent on the skill of the operator, CNC lathes offer greater precision in the operation of machining parts. Even so, the CNC requires that the operator have machining cores, tools and materials and above all programming either by conversational machine or CAM.
Ideal for large series of pieces: Due to its characteristics, the CNC lathe is emerging as the most efficient machine for large series, with the extra advantage of being able to execute geometries of greater complexity than a conventional lathe depending on its configuration (motorized tool, Y axis, B axis among others options) in addition to offering different automation options that allow the autonomous work of the machine, such as bar feeder, pick up parts and parts loader among others.
Possibility of simultaneous cutting operation: CNC lathes, in addition, can work simultaneously with various cutting tools, both static and motorized. With one or multiple tool turrets that can work simultaneously or independently.
In another post we will specify in more depth the types of CNC lathe, their functions and the different options they allow
Recent Comments